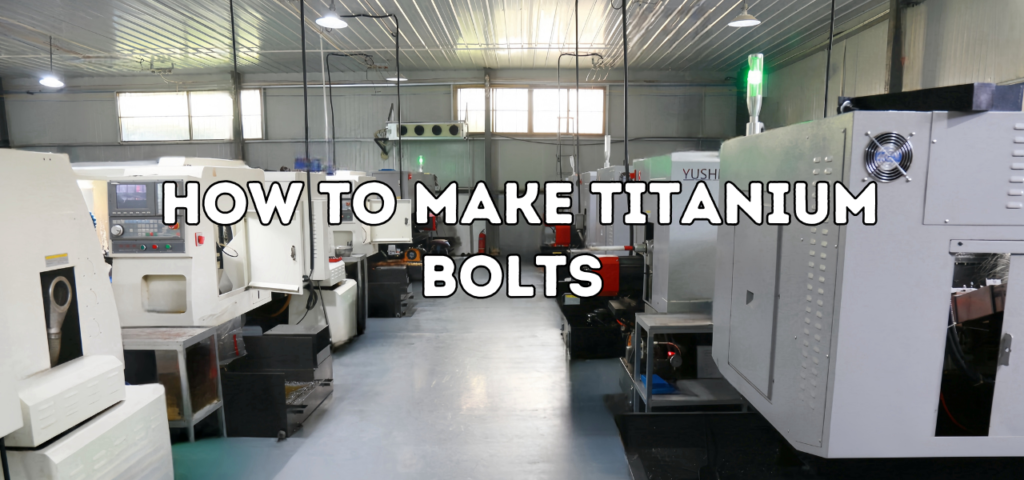
How to make titanium bolts? As a professional titanium bolts manufacturer, we have 10 years of manufacturing experience, in this article, we briefly talk about how to make titanium bolts.
Titanium Bolts Material Preparation
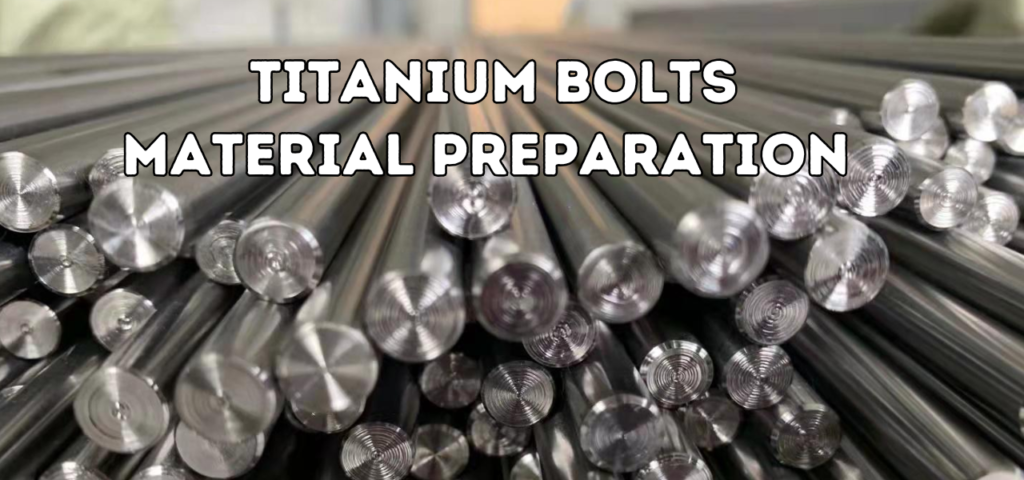
At the storage stage of raw materials, IQC performs batch verification of titanium alloy bars to check the alloy composition, heat treatment state and mechanical properties parameters in the material certificate. Non-destructive testing equipment is used to scan the surface of the material and remove defective materials with scratches, pits or oxide layers.
We calculate the blanking length according to the bolt specification, and use precision cutting equipment for fixed length cutting to ensure that the flatness of the incision meets the requirements of subsequent processing.
Key Considerations of Material Preparation
Operators must physically isolate titanium cutting zones from steel processing areas using dedicated ventilation systems and tooling, while implementing magnetic sweeps to remove residual iron filings that could compromise titanium’s corrosion resistance.
During the cutting process, the friction heat should be controlled to prevent the local temperature from causing the material to harden.
Material handlers shall:
Wrap cut billets in VCI (Vapor Corrosion Inhibitor) paper within 30 minutes post-cutting
Transfer sealed batches to CNC machining within 18 hours (not 24)
Record storage time/temperature in MES system for traceability
Hot Heading of Titanium Bolts

The operator sends the cut billet into the heating furnace and heats it to the plastic deformation temperature range of titanium alloy in a protective atmosphere.
After heating titanium billets to 900-950°C, forging crews:
① Rapidly transfer them to preheated dies (300-350°C)
② Sequence through multi-station presses for pre-forging → final forging → shaping
③ Immediately water-quench workpieces to lock fine grain structures.
Key Considerations of Hot Heading
The heating temperature should be controlled precisely. Insufficient temperature will lead to molding cracking, and too high temperature will cause grain coarsening.
The mold must be preheated to the specified temperature in advance to prevent thermal stress cracks caused by cold mold contact with high temperature billet.
During the molding process, the inert gas should be continuously purged to avoid the surface oxidation of titanium to form α embrittlement layer.
Titanium Bolts Machining

Shank Precision Turning
Machinists process hot-forged shanks using ultra-hard tools: Stage 1: Remove bulk material with aggressive rough cuts Stage 2: Achieve ±0.01mm accuracy via high-speed/low-feed finishing Process Control: Continuously spray high-pressure coolant while tracking tool wear via sensors
Key Considerations of Shank Precision Turning
Avoid using chipped tools to prevent surface scaling defects.
Insufficient coolant flow causes heat buildup and α-case formation.
Perform full-dimension inspection on the first piece of each batch.
Head Feature Machining
Hex heads are milled via multi-axis interpolation with layer-by-layer cutting (depth per layer
≤1/3 of tool diameter). For internal hex sockets: pre-drill with stepped drills, then form threads via spiral-flute tapping, followed by ultrasonic cleaning to remove debris.
Key Considerations of Head Feature Machining
Clamp workpiece securely during milling to prevent edge chipping.
Verify hole size before tapping – interference >0.05mm risks tap breakage.
Inspect socket bottoms with magnifier after cleaning.
Transition Zone Treatment
Machine radius transitions at head-shank junctions using forming tools with three-stage refinement:
90% material removal in first pass
Surface roughness optimization in second pass
Mirror finish via micro-feeding in third pass.
Key Considerations of Transition Zone Treatment
Transition radius must ≥15% of shank diameter to avoid stress concentration.
Replace coolant with alcohol wiping during finishing to prevent contamination.
Perform fluorescent penetrant inspection after machining.
Thread Machining of Titanium Bolts

The thread is processed by cold rolling process. Technicians position the heat-treated bolt shank between rolling dies, then apply radial pressure to plastically deform the material into precise thread profiles. After processing, use compressed air to clean the metal debris in the thread groove, and carry out a full check of the pass and stop gauge.
Key Considerations of Thread Machining
It is necessary to calibrate the coaxiality of the die before rolling, and the deviation of more than 0.05mm will lead to the asymmetry of the thread teeth.
Special titanium alloy processing oil without chlorine should be selected as lubricant to prevent stress corrosion.
Operators monitor the pressure curve in real time during thread rolling, where sudden pressure drops signal potential internal material defects.
Titanium Bolts Surface Treatment
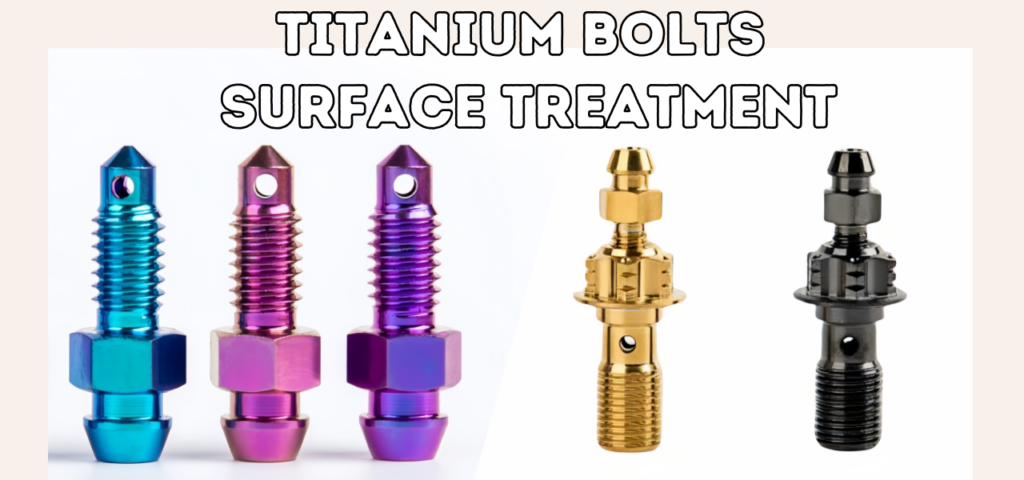
Titanium Bolts Anodizing
Workers perform titanium bolt anodizing through an electro-chemical process, applying DC voltage in the electrolyte to form a protective oxide film on the titanium alloy surface. The oxide film has good wear resistance, corrosion resistance and decorative properties.
Titanium Bolts PVD
PVD (Physical vapor deposition) is a physical coating technology that forms a thin film by vaporizing and depositing a metal or compound on the surface of a titanium bolt in a vacuum environment. The film has high hardness, high wear resistance and good chemical stability.
Quality Inspection of Titanium Bolts
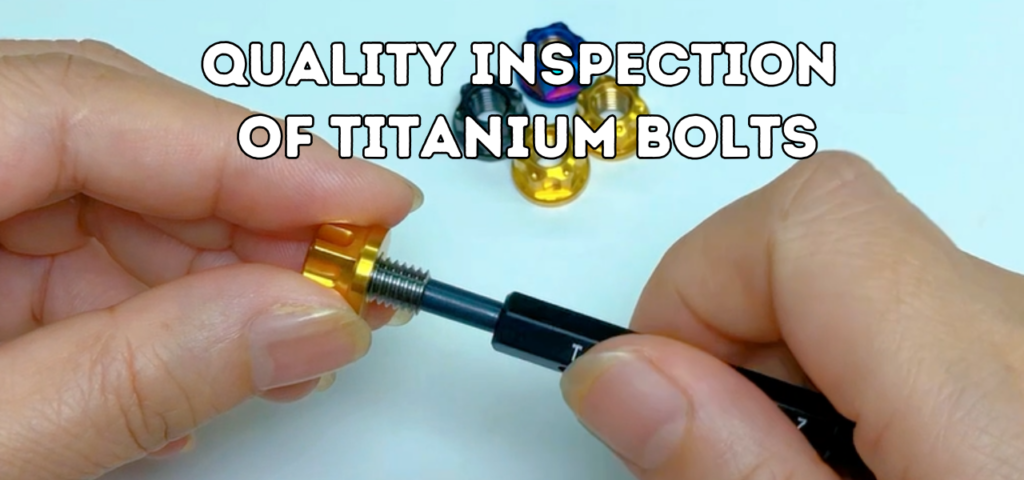
Implement a three-level inspection system:
First full size measurement (including thread diameter, tooth profile Angle and head thickness)
Torque testing and metallographic analysis according to AQL sampling standards in mass production
100% visual inspection of surface defects and magnetic particle detection (for iron contamination screening) before final shipment.
Key Considerations of Quality Inspection
Operators should regularly calibrate the measuring tool with a standard measuring block to prevent the accumulation of errors in the measuring system.
The samples in the salt spray test chamber should be placed at a tilt Angle of 20° to ensure uniform adhesion of corrosive liquid.
The lighting intensity of the detection area should be ≥1000 lux to avoid missing subtle surface defects.
Conclusion
The manufacture of titanium bolts is a complex and delicate process. Its involving multiple links from material preparation to surface treatment, each with its own specific operational flow and key considerations. Precise process control and strict quality inspection are the key to ensure that titanium bolts meet high performance requirements.
Need titanium bolts manufacturer, contact us for titanium standard bolts and custom titanium fasteners.
- How Much Weight Do Titanium Bolts Save?
- Why GR5 Bolts Are the Top Choice for High-Performance Fastening Solutions
- How Strong Are Titanium Bolts? Ultimate Guide to Their Tensile Strength & Applications
- FAQs About Custom Titanium Bolts: Strength, Cost, and Customization Options
- Titanium Lug Nuts Compatibility: How to Match Thread Size, Pitch, and Seat Type